Cement Market Size:
The global cement market size reached US$ 385.8 Billion in 2023. Looking forward, IMARC Group expects the market to reach US$ 629.9 Billion by 2032, exhibiting a growth rate (CAGR) of 5.4% during 2024-2032. The global cement market is witnessing robust growth driven by rapid urbanization, infrastructure development, favorable government initiatives and policies, rising disposable incomes, and increasing construction activities, especially in emerging economies.
Report Attribute
|
Key Statistics
|
Base Year
|
2023
|
Forecast Years
|
2024-2032
|
Historical Years
|
2018-2023
|
Market Size in 2023
|
US$ 385.8 Billion |
Market Forecast in 2032
|
US$ 629.9 Billion |
Market Growth Rate 2024-2032 |
5.4% |
Cement Market Analysis:
- Major Market Drivers: Based on the cement market growth report, key drivers include growing population and urbanization, implementation of various government initiatives and policies, widespread expansion of the retail sector, and rising disposable income of consumers.
- Key Market Trends: The cement industry overview highlights several trends in the market, such as the increasing adoption of green cement, which offers reduced carbon footprints and superior sustainability. Beyond this, the growing inclination towards modular construction practices, which utilize precast cement products, is fueling the market growth.
- Geographical Trends: According to the cement industry research report, Asia-Pacific is the dominant region due to massive construction activities, rapid urbanization, industrial expansion, and significant infrastructure investments. Other regions are also showing significant growth because of the ongoing renovation and maintenance of existing infrastructure and growing urban populations.
- Competitive Landscape: Some of the major market players in the cement industry include China National Building Materials Group Corporation, Holcim Ltd, Anhui Conch Cement Co., Ltd., Jidong Development Group Co., Ltd. and Heidelberg Materials, among many others.
- Challenges and Opportunities: The recent cement industry outlook describes various challenges, such as high energy consumption, carbon emissions, and the need for raw material sourcing, which can impact the environment significantly. However, these challenges also present opportunities for market players to invest in research and development (R&D) to improve production efficiency.
Cement Market Trends:
Growing population and rapid urbanization
The rapid population growth and urbanization across the globe are primary drivers boosting the cement market share. According to the United Nations, the world's population is predicted to grow by approximately 2 billion over the next 30 years. Expanding global population has led to the heightened need for infrastructure and housing, which extensively utilize cement for various construction projects. Furthermore, the United Nation has predicted that global urban population will increase to two-third by 2050. This rising trend necessitates the development of new cities, roads, bridges, and other infrastructure projects, which increases the cement market share. Moreover, the heightened need to accommodate a growing population and provide suitable living and working conditions is promoting the global cement market growth.
Government initiatives and investments in infrastructure projects
According to the cement industry research report, governments across globe are acknowledging the value of infrastructure development for economic growth and social well-being. In line with this, they are allocating considerable resources to create and improve transportation networks, including roads, highways, trains, and airports. For example, the US Department of Transportation revealed in 2022 that public and private investment in transportation infrastructure and equipment reached $403.9 billion, accounting for 7.4 percent of the overall investment of $5,476.1 billion. Moreover, the heightened investment in these activities creates the need for vast volumes of cement to build long-lasting and dependable infrastructure, boosting the adoption of efficient and durable cement. Furthermore, the introduction of various requirements that stimulate the use of ecologically friendly cement, consequently increasing the growth rate of green cement to (CAGR) 10.7% between 2024 and 2032, is propelling the market growth.
Expanding real estate sector
According to the cement industry overview, the rising real estate sector is another key driver strengthening the global cement market growth. As economies expand and wages rise, so does the demand for houses, commercial properties, and other real estate assets. According to the IMARC analysis, the real estate industry is predicted to reach $8,654 billion by 2032, growing at a 1.9% CAGR from 2024 to 2032, leading to an increase in building activity. Residential, commercial, and industrial buildings are among the many areas of the real estate industry that require cement for foundations, walls, floors, and other structural parts. Furthermore, urbanization, population increase, and changing lifestyles add to the need for contemporary and visually pleasing structures, boosting the market growth.
Cement Market Segmentation:
IMARC Group provides an analysis of the key trends in each segment of the market, along with forecasts at the global, and regional levels for 2024-2032. Our report has categorized the market based on type and end use.
Breakup by Type:
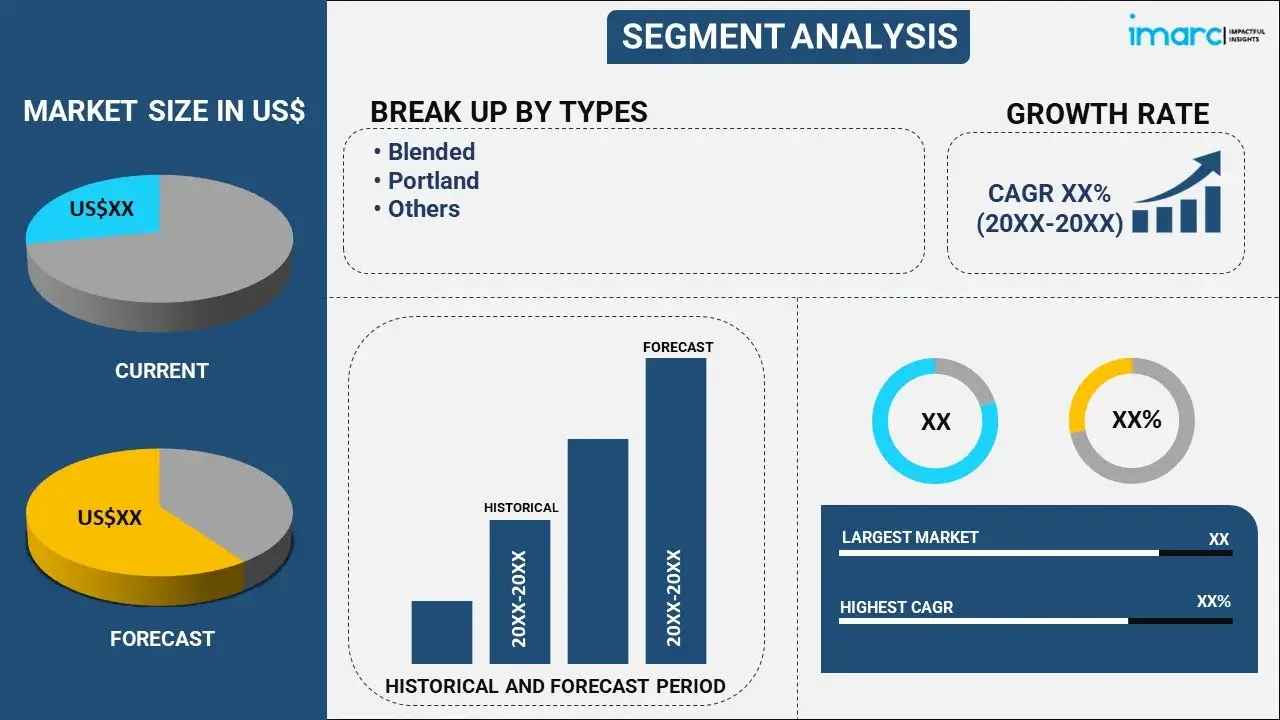
Portland accounts for the majority of the market share
The report has provided a detailed breakup and analysis of the market based on the type. This includes blended, Portland, and others. According to the report, Portland represented the largest segment.
According to the cement industry research report, Portland cement dominates the market owing to its great durability and strength, making it suitable for a variety of building applications. The IMARC Group projects that the Portland cement industry will reach 3.1 billion tons by 2032, with a 3.2% compound annual growth rate (CAGR) from 2024 to 2032. The growing popularity of the product, that possesses a high compressive strength and is capable of handling huge loads and adverse weather conditions, is boosting the cement market share. It is also adjustable in terms of composition, allowing for changes to meet specific project requirements. Furthermore, Portland cement has faster hardening and setting durations than other cement types, reducing manufacturing time and increasing efficiency.
Breakup by End Use:
- Residential
- Commercial
- Infrastructure
Residential holds the largest share of the industry
A detailed breakup and analysis of the market based on the end use has also been provided in the report. This includes residential, commercial, and infrastructure. According to the report, residential accounted for the largest market share.
In line with the global cement industry statistics, the residential segment leads the market due to several significant characteristics, including rising housing demand, which is being driven by population expansion, rapid urbanization, and increasing disposable incomes. Residential building projects, which include single-family houses, apartments, and condominiums, provide a substantial contribution to the global cement market growth. Furthermore, residential constructions require a huge quantity of cement for their foundations, roofing, flooring, and other structural components, which serves as a key driver stimulating the market growth. Along with this, cement's strength, durability, and adaptability make it an excellent choice for constructing safe and long-lasting residential building projects.
Breakup by Region:
.webp)
- Asia Pacific
- North America
- Europe
- Latin America
- The Middle East and Africa
Asia Pacific leads the market, accounting for the largest cement market share
The report has also provided a comprehensive analysis of all the major regional markets, which include North America, Europe, Asia Pacific, Latin America, and the Middle East and Africa. According to the report, Asia Pacific represents the largest regional market for cement.
In accordance with cement market growth report, the Asia Pacific region is quickly expanding due to its fast-growing population, resulting in increased urbanization and infrastructure development. Furthermore, certain Asia Pacific countries, including China, India, and Japan, have had strong economic growth in recent years, bolstering the need for cement in the construction industry. For example, in FY23, India's residential property market saw home sales reach an all-time high of Rs. 3.47 lakh crore (US$ 42 billion), reflecting a strong 48% year-on-year increase. Furthermore, rising demand for residential, commercial, and public infrastructure projects such as roads, bridges, and airports is propelling the global cement industry growth. In line with this, IMARC Group expects the Japan's condominium and apartment market size to exhibit a growth rate (CAGR) of 4.23% during 2024-2032, boosting the demand for cement.
Competitive Landscape:
- The market research report has also provided a comprehensive analysis of the competitive landscape in the market. Detailed profiles of all major companies have also been provided. Some of the major market players in the cement industry include China National Building Materials Group Corporation, Holcim Ltd, Anhui Conch Cement Co., Ltd., Jidong Development Group Co., Ltd., Heidelberg Materials, etc.
- According to the cement industry price trend, the market is intensely competitive, due to the existence of huge international corporations, regional rivals, and small-scale manufacturers. To maintain a competitive edge, cement companies use strategies, such as mergers and acquisitions, product innovation, and regional expansion. Mergers and acquisitions allow companies to consolidate market share, get access to new technologies, and expand their customer base. Furthermore, they prioritize research and development (R&D) initiatives to increase the quality and sustainability of their cement products. Furthermore, cement companies are investing in ecologically friendly procedures and developing low-carbon cement solutions to decrease carbon dioxide (CO2) emissions during manufacturing.
Cement Market News:
- On May 24, 2023, China National Building Material (CNBM) Group launched a high-performance carbon fiber project with an annual output of 25,000 tons.
- On November 14, 2023, Holcim announced the successful completion of its 36,804,453 shares buyback programme.
- On September 22, 2022, HeidelbergCement changed its name to Heidelberg Materials. It aims to be the first company to offer carbon-free cement on large-scale projects by 2024.
Cement Market Report Scope:
Report Features |
Details |
Base Year of the Analysis |
2023 |
Historical Period |
2018-2023 |
Forecast Period |
2024-2032 |
Units |
Billion Tons, US$ Billion |
Scope of the Report |
Exploration of Historical and Forecast Trends, Industry Catalysts and Challenges, Segment-Wise Historical and Predictive Market Assessment:
|
Types Covered |
Blended, Portland, Others |
End Uses Covered |
Residential, Commercial, Infrastructure |
Regions Covered |
Asia Pacific, Europe, North America, Latin America, Middle East and Africa |
Companies Covered |
China National Building Materials Group Corporation, Holcim Ltd, Anhui Conch Cement Co., Ltd., Jidong Development Group Co., Ltd., Heidelberg Materials, etc.
(Please note that this is only a partial list of the key players, and the complete list is provided in the report.) |
Customization Scope |
10% Free Customization |
Report Price and Purchase Option |
Single User License: US$ 3899
Five User License: US$ 4899
Corporate License: US$ 5899 |
Post-Sale Analyst Support |
10-12 Weeks |
Delivery Format |
PDF and Excel through Email (We can also provide the editable version of the report in PPT/Word format on special request) |
Key Benefits for Stakeholders:
- IMARC’s report offers a comprehensive quantitative analysis of various market segments, historical and current market trends, market forecasts, and dynamics of the cement market from 2018-2032.
- The research study provides the latest information on the market drivers, challenges, and opportunities in the global cement market.
- The study maps the leading, as well as the fastest-growing, regional markets.
- Porter's five forces analysis assist stakeholders in assessing the impact of new entrants, competitive rivalry, supplier power, buyer power, and the threat of substitution. It helps stakeholders to analyze the level of competition within the cement industry and its attractiveness.
- Competitive landscape allows stakeholders to understand their competitive environment and provides an insight into the current positions of key players in the market.